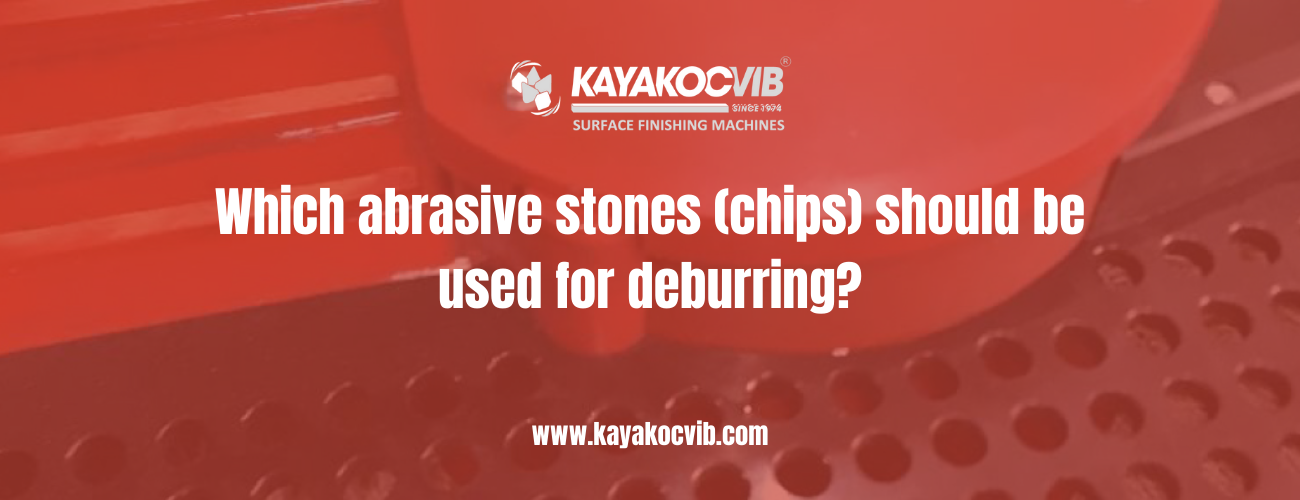
08 Nov Which abrasive stones (chips) should be used for deburring?
The selection of the most suitable abrasive stone for the product is made according to two different criteria.
1- The raw material of the product or the type of metal used:
Stones with different abrasiveness are produced for metals with different hardness. For example, plastic abrasive stones are suitable for low-strength metal products such as aluminum, while ceramic abrasive stones should be used for high-strength metals such as stainless steel. Thus, the proportion of application time x in the surface accuracy equation is set correctly. Otherwise, high-abrasive stones can have negative results on low-strength metals, while low-abrasive stones create a very long process time in high-strength products.
2- Geometric structure of the product
The products naturally have very variable geometric structures, so the geometric structures of the abrasive stones also vary widely. The most important issue during the process is that the stone can reach all surfaces of the product. Thus, the most accurate result is obtained.
What fluids should be used in deburring?
The liquids used in the deburring process are of two types and are selected depending on the raw material of the products as in the selection of abrasive stones. These are “degreasing” and “deburring” liquids. Surface treatment fluids have different pH and acidity levels, but they also contain anti-corrosion additives. As the pH rises, the effect of the liquid changes on the product. That’s why choosing the right fluid is so important. Water is the third liquid used at every stage. Also, the last rinse is done only with water. Surface treatment fluids do not leave residue or residue on the product thanks to their special ingredients.
How to determine the deburring process time?
The deburring process time is determined by checking the products that are applied for the first period during the process. Since the burrs are of varying levels, each different product is processed at different times, so time should be checked at the first application of each new product. The surface treatment application continues until all burrs disappear and the surface of the product reaches the desired homogeneous structure. For example, with the controls performed every 15 or 30 minutes, the final processing time of the product can be determined. The processing time determined afterward can be repeatedly applied to other products of the same type and type.
How is polishing done?
The polishing stage is the third surface treatment application. The products that come out of the burring process are subjected to the polishing process and the surface that is smoothed is also polished. Many products in different sectors are used quite often because they are polished and presented to the end user or prepared for the next process. The polishing phase is also an application that supports the product in terms of cosmetics. Polishing has become mandatory before some coating processes. The polishing process consists of two stages, polishing, and rinsing. During the process, polishing stones called “Porcelain” are used. Porcelain stones, which have many types in size and shape, are selected again according to the geometric structure and size of the product. Although porcelain polishing stones have very low deburring properties, their lifespan is many times more than the of deburring stones. KAYAKOCVIB deburring fluids also have a polishing effect. Therefore, the same surface treatment fluid is used in both deburring and polishing processes. The polishing phase is completed in a much shorter time than the deburring phase as the processing time. The polished products are transferred to the next and final stage, ‘Drying’.
How is the drying process done?
The drying stage is the fourth surface treatment application and the final stage. The products that are degreased, burrs, and polished differ depending on the raw material of the product and subsequent application, to protect it from corrosion and other effects, it is cleaned from water, and moisture and the process is terminated. In some coating applications, products that come out of the polishing by skipping the drying process are sent directly to the coating. The drying process is carried out in the dryer vibration machine with the help of corn granules (corn cob granules) and resistances. The Dryer Vibratory Machine transfers the granules to the specified heat thanks to its resistance. Thanks to the moisture absorption feature of the granules, all surfaces of the product are dehumidified. The moisture trapped in the granules is clouded thanks to the heat and the granules are dried again. Granules also have two additional features, such as light degreasing and polishing.
Choosing the Right Abrasive Stones for Your Deburring Needs
At Kayakoç VIB, we understand the frustration of pesky burrs ruining your finished product’s quality and aesthetics. The perfect abrasive stone awaits, ready to tame those unwanted metal shards and leave your surfaces smooth as silk. But with so many options, choosing the right one can feel like navigating a maze blindfolded. Worry no more, for this guide will be your compass, leading you to the ideal abrasive stone for your deburring needs.
Hardness Matters: Matching Stone to Metal
The first rule of deburring is understanding the hardness dance between your abrasive stone and the metal you’re working with. Here’s a breakdown:
Soft Metals (Aluminum, Magnesium): Gentle giants like silicon carbide or diamond-impregnated stones are your allies. They’ll remove burrs without gouging or damaging the delicate surface.
Medium-Hard Metals (Mild Steel, Brass): Aluminum oxide is your go-to warrior. It’s tough enough to tackle stubborn burrs while remaining kind to the metal.
Hard Metals (Stainless Steel, Titanium): Bring out the heavy hitters! Ceramic or CBN (cubic boron nitride) stones will conquer even the most tenacious burrs on these tough metals.
Beyond Hardness: Shape and Size
The shape and size of your stone are crucial for reaching those nooks and crannies where burrs love to hide. Here’s a quick cheat sheet:
Cylindrical stones: Ideal for general deburring on flat surfaces or curved edges.
Ball-shaped stones: Perfect for reaching tight corners and internal crevices.
Cone-shaped stones: Great for removing burrs from inside holes and narrow channels.
Disc-shaped stones: Versatile for both flat surfaces and contoured areas.
Grit: A Matter of Precision
The grit size of your stone determines the level of finishing you’ll achieve. Coarse grits (80-120) efficiently remove large burrs, while finer grits (220-320) leave a smoother, more polished surface. Remember, start rough and gradually move to finer grits for a flawless finish.
Bonus Tip: Consider the Coolant
Metalworking generates heat, and heat can be detrimental to both your stone and the workpiece. Using a coolant like water or oil will keep things cool, prolonging the life of your stone and preventing warping of the metal.
Kayakoç VIB: Your Deburring Partner
At Kayakoç VIB, we offer a diverse range of abrasive stones and chips to suit every deburring need. Whether you’re a seasoned pro or a curious beginner, our experts are here to guide you to the perfect match. So, ditch the frustration and embrace the smooth satisfaction of a burr-free finish. Visit Kayakoç VIB today and conquer those pesky burrs like a true metalworking champion!
Keywords: abrasive stones, deburring, metalworking, Kayakoç VIB, aluminum, steel, stainless steel, silicon carbide, aluminum oxide, ceramic, CBN, grit, coolant
No Comments