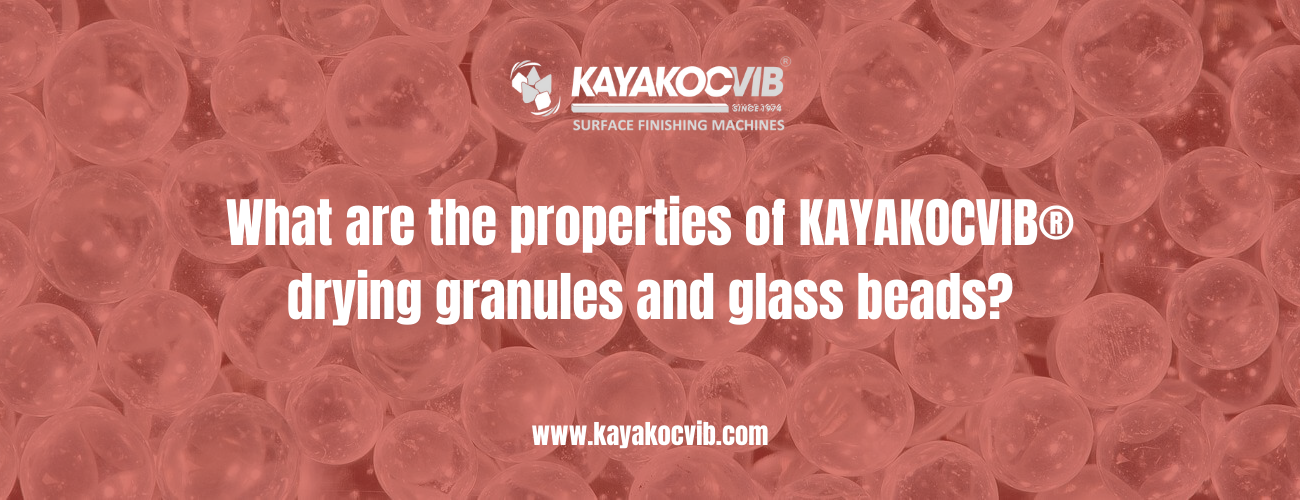
18 Nov What are the properties of KAYAKOCVIB® drying granules and glass beads?
Revolutionize your metal finishing with our vibratory dryers’ drying granules, meticulously crafted from maize plants. These specialized granules are tailored for drying wet metal surfaces, enhancing corrosion resistance for components emerging from the vibration process. With various sizes available, you can select granule particle sizes that precisely match your material needs.
Our drying vibratory machines not only accelerate the drying process but also contribute to a polished surface through surface rubbing. What sets our granules apart is their dust-free composition, ensuring surfaces remain pristine without any residue. Packaged conveniently in 20 kg bags, our drying granules offer a clean and efficient solution for your metal finishing needs. Elevate your metal surface treatment with our cutting-edge technology, where maize-derived drying granules redefine the standards of corrosion resistance and surface polish. Opt for excellence in metal finishing with our innovative and dust-free drying granules.
The sizes of KAYAKOCVIB drying granules:
CODE | SIZES | MICRONS |
MG 04 | 6,5 – 8,0 mm | 6500 – 8000 microns |
MG 06 | 3,5 – 6,5 mm | 3500 – 6500 microns |
MG 08 | 2,5 – 3,5 mm | 2500 – 3500 microns |
MG 10 | 1,6 – 2,5 mm | 1600 – 2500 microns |
MG 12 | 1,0 – 2,0 mm | 1000 – 2000 microns |
MG 16 | 0,8 – 1,5 mm | 800 – 1500 microns |
MG 20 | 0,6 – 1,0 mm | 600 – 1000 microns |
MG 30 | 0,25 – 0,8 mm | 250 – 800 microns |
MG 80 | 0,18 – 0,6 mm | 180 – 600 microns |
WALNUT AND PECAN GRANULES
They are used in various applications especially in the jewelry industry. Various grit sizes are available. They are available in bags of 20 kg.
ABRASIVE-POLISHING PASTE AND ABRASIVE GRANULES
PURPOSE OF PASTE
It is the vibration auxiliary consumable used for obtaining a surface close to the polishing quality according to the standard polishing process. It also increases the deburring speed on vibratory machines. There are various compositions for faster abrasion. Abrasive granules are particles used for surface grinding or for creating roughness on the surface. Various grit sizes are available. Please contact us for usage and quantity. They are available in containers of 20 kg.
GLASS BEADS
They are micro-particles that prevent flat and smooth surfaces from sticking together. They separate the parts that may stick or touch each other in the vibratory machines, during the tumbling process. They are selected in different microns according to the application. They are available in carton pouches of 25 kg.
What are Granules?
Granules are small, often microscopic particles or pellets that are formed by aggregating fine particles together. These particles can be of various materials, including but not limited to minerals, polymers, pharmaceutical substances, and agricultural compounds. The formation of granules typically involves a process known as granulation, where smaller particles are bound together to create larger, more cohesive structures.
Drying Beads
Drying beads, often referred to as desiccant beads, are unsung heroes in various industries, silently working to maintain optimal moisture levels and protect valuable products. In this article, we will explore the ins and outs of drying beads, their uses, and how they can be a game-changer in preserving the integrity of diverse materials.
Applications of Drying Beads
1. Preservation of Pharmaceuticals: In the pharmaceutical industry, maintaining the stability and efficacy of drugs is paramount. Drying beads play a crucial role in pharmaceutical packaging by preventing moisture-induced degradation, ensuring the longevity and effectiveness of medications.
2. Electronics Protection: Sensitive electronic components are highly susceptible to moisture damage. Drying beads are often incorporated into packaging for electronics, safeguarding devices from corrosion and malfunctions caused by excess humidity.
3. Food Storage and Packaging: In the food industry, preventing moisture is essential to preserving the quality of products. Drying beads help extend the shelf life of packaged foods by creating a dry environment that inhibits the growth of mold and bacteria.
Advantages of Using Drying Beads
1. Reusability: Certain types of drying beads, especially those made from molecular sieves, can be regenerated and reused, making them a cost-effective solution for long-term applications.
2. Versatility: Drying beads come in various sizes and materials, offering versatility in their applications. From small silica gel packets in product packaging to large-scale industrial drying units, these beads can adapt to different moisture control needs.
What are Abrasive Granules?
Abrasive granules are small, hard particles used for their abrasive qualities in industrial processes. These granules can be composed of diverse materials such as minerals, ceramics, and even metals. The primary purpose of abrasive granules is to wear away or alter the surface of materials through a process known as abrasion.
Types of Abrasive Granules:
1. Natural Abrasives: Derived from natural sources, such as minerals and rocks, natural abrasive granules include materials like diamond, garnet, and pumice. Diamond, in particular, is renowned for its hardness and is widely used for precision cutting and grinding.
2. Synthetic Abrasives: Engineered for specific applications, synthetic abrasive granules include materials like aluminum oxide, silicon carbide, and fused alumina. These abrasives offer consistent quality and performance, making them popular choices in industrial settings.
3. Bonded Abrasives: In bonded abrasives, the abrasive granules are held together by a bonding agent. This category includes grinding wheels and abrasive discs commonly used in metalworking and surface finishing.
4. Coated Abrasives: Coated abrasives involve applying abrasive granules to a flexible backing material. Sandpaper is a familiar example of coated abrasives, serving purposes from woodworking to automotive refinishing.
Applications of Abrasive Granules:
1. Metalworking: In metal fabrication and machining, abrasive granules are employed for tasks like grinding, deburring, and polishing. They play a crucial role in shaping and refining metal surfaces.
2. Woodworking: Abrasive granules find applications in woodworking for tasks like sanding and shaping wooden surfaces. From hand sanding to machine-based processes, abrasives contribute to achieving smooth and refined wood finishes.
3. Precision Machining: Industries involved in precision machining, such as aerospace and automotive, rely on abrasive granules for achieving tight tolerances and fine surface finishes in components.
Advantages of Abrasive Granules:
1. Precision and Consistency: Abrasive granules offer precision in material removal, allowing for controlled and consistent results across various applications.
2. Versatility: The diverse types of abrasive granules cater to a wide range of materials and applications, making them versatile tools in industrial processes.
How Do You Dry Glass Beads?
Drying glass beads effectively is a crucial step in ensuring their quality and performance in various applications. Whether you are in the jewelry-making industry, using glass beads for crafting, or employing them in industrial processes, understanding the right methods for drying is essential.
Importance of Proper Drying
1. Prevention of Water Stains: Glass beads are susceptible to water stains, which can diminish their clarity and overall visual appeal. Proper drying methods help prevent these stains, ensuring that your glass beads retain their pristine appearance.
2. Preservation of Quality: Effective drying contributes to preserving the quality of glass beads, preventing potential damage caused by prolonged exposure to moisture.
Techniques for Drying Glass Beads
1. Air Drying: Place the glass beads on a clean, dry surface and allow them to air dry naturally. Ensure proper ventilation to speed up the drying process. This method is suitable for beads that are not overly delicate or sensitive to prolonged exposure to air.
2. Towel Drying: Gently pat the glass beads with a soft, lint-free towel to absorb excess moisture. Take care to avoid rubbing, as this can cause scratches. Towel drying is effective for quickly removing surface water.
3. Use of Desiccants: Place glass beads in a container with a desiccant, such as silica gel or other moisture-absorbing materials. Desiccants help expedite the drying process by actively absorbing moisture from the surrounding environment.
4. Blow Drying: Use a hair dryer on a low or cool setting to gently blow dry the glass beads. Keep a safe distance and avoid using high heat to prevent thermal shock or damage to the beads. This method is effective for quickly drying beads without leaving water spots.
Tips for Effective Drying
1. Gentle Handling: Handle glass beads with care to avoid scratches or damage during the drying process. Use soft materials and gentle movements to ensure the beads remain in pristine condition.
2. Prompt Drying: Dry glass beads promptly after any exposure to moisture. This helps prevent water stains and ensures the beads maintain their original quality.
3. Controlled Environment: Choose a controlled environment with low humidity for drying glass beads. This minimizes the risk of water stains and promotes a more efficient drying process.
What Grit is Glass Bead?
Grit levels play a pivotal role in determining how these beads perform, from surface preparation to finishing touches.
Defining Grit in Glass Beads
1. Understanding Grit Numbers: Grit levels are denoted by numerical values, indicating the size of the glass beads. Higher numbers represent finer grit, while lower numbers signify coarser grit. For instance, a grit of 80 is coarser than a grit of 120.
2. Particle Size Variation: Glass beads come in a range of grit sizes, allowing for versatility in applications. The variation in particle size affects the abrasive action of the beads, influencing factors like surface texture and finish.
Common Grit Levels and Applications
1. Coarse Grit (30-80): Coarse grit glass beads are ideal for tasks that require substantial material removal, such as cleaning surfaces with heavy coatings or rust. These beads are effective in preparing surfaces for subsequent treatments.
2. Medium Grit (80-150):Medium grit glass beads strike a balance between material removal and surface refinement. They are commonly used in applications like deburring, smoothing, and preparing surfaces for painting or coating.
3. Fine Grit (150-220): Fine grit glass beads excel in providing a smooth finish without significant material removal. They are suitable for polishing and achieving a refined surface texture, making them valuable in jewelry making and precision finishing.
4. Extra Fine Grit (220+): Extra fine grit glass beads are employed for intricate work where a high level of precision and a polished finish are essential. These beads are often used in the final stages of surface preparation for a flawless appearance.
Choosing the Right Grit for Your Project
1. Consider the Material: The material you are working with influences the choice of grit. Coarser grits are suitable for tougher materials, while finer grits are preferred for delicate or softer surfaces.
2. Desired Finish: Determine the level of surface finish you aim to achieve. Coarser grits create textured surfaces, while finer grits result in smoother, polished finishes.
3. Application Specifics: Tailor your choice of grit to the specific task at hand. Whether it’s paint removal, surface preparation, or intricate detailing, selecting the right grit ensures optimal results.
No Comments