Covering |
Chemical Composition |
Colour |
Sertlik (HV 0.05) |
Friction coefficient (against steel) |
Thickness (μm) |
Oxidation/ Decomposition Temperature(°C) |
General Characteristics |
Mold Application Suggestions |
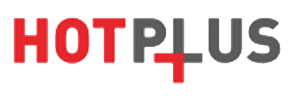 |
AlTiCrN |
Dark grey |
3600±400 |
0,4 |
2 – 8 |
900°C |
High hardness, high toughness, good high temperature resistance |
In high pressure aluminum injection cores, aluminum extrusion die-tenon and hot forming cores |
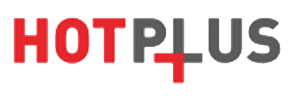 |
AlCrN |
Light grey |
3600±300 |
0,5 |
2 – 5 |
1000°C |
High hardness, high hot hardness, very good high temperature resistance |
High pressure aluminum injection insert-core, in hot forming cores |
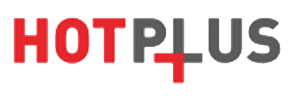 |
TiAlN |
Dried rose |
2800±200 |
0,4 |
4 – 8 |
800°C |
High toughness and high hot hardness, low coefficient of friction and high applicability of coating thickness |
In high pressure aluminum and zamak injection cores, pin, insert-core, hot forming cores |
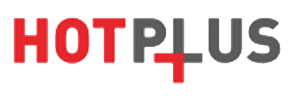 |
ZrN |
Light yellow |
3000±200 |
0,35 |
2 – 5 |
600°C |
Excellent surface properties, very high adhesive wear resistance, very good corrosion resistance |
In high pressure magnesium injection |
FEXOY
|
Diffusion Process + FeO |
Dark black |
1150± 50 |
– |
12 – 15 |
– |
Dark black Abrasion resistance and solid lubricating surface properties Diffusion Process |
Press hot forging dies, Metal injection sleeves |
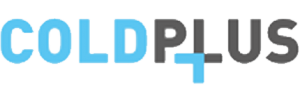 |
TiN |
Gold yellow |
2600±200 |
0,5 |
2 – 4 |
600°C |
General purpose use, wide application area, all mechanicalchemical properties are moderate |
In cutting (if the workpiece is iron-based) molds |
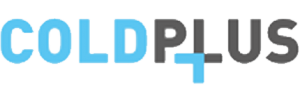 |
CrN |
Silver grey |
2100±200 |
0,35 |
2 – 8 |
600°C |
High toughness, corrosion resistance, low coefficient of friction |
Forming molds |
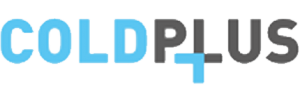 |
TiCN |
Magenta-grey |
3800±200 |
0,25 |
2 – 4 |
400°C |
High hardness, high wear resistance and low friction coefficient, improved toughness, lubricating properties |
Cutting, forming molds |
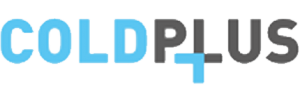 |
TiCrN |
Dark golden yellow |
3400±200 |
0,35 |
2 – 5 |
600°C |
Excellent toughness, low coefficient of friction, high hardness, high resistance to workpiece sticking and wrapping |
Deep drawing, forming molds |
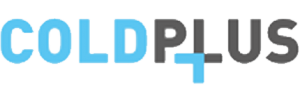 |
AlCrN |
Light grey |
3600±200 |
0,5 |
1 – 4 |
1000°C |
High hardness, high hot hardness, high oxidation resistance |
In cutting (precision, dry cutting) molds |
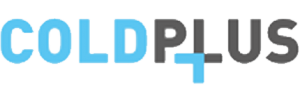 |
AlTiN |
Anthracite |
3400±200 |
0,75 |
2 – 6 |
900°C |
High hardness, high toughness, high temperature resistance, high hot hardness |
In cutting, plucking cutting, forming mold |
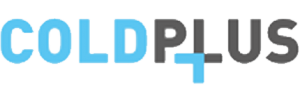 |
ZrN |
Light yellow |
3000±200 |
0,35 |
2 – 5 |
600°C |
Excellent surface properties, very high adhesive wear resistance, very good corrosion resistance. |
Forming (if the workpiece is non-ferrous based) molds |
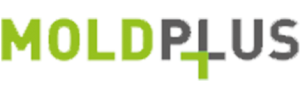 |
TiN |
Gold yellow |
2600±200 |
0,5 |
2 –4 |
600°C |
General purpose use, wide application area, all mechanicalchemical properties are moderate |
Plastic injection mold, pin, pusher, scrapers |
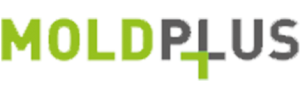 |
CrN |
Silver grey |
2100±200 |
0,35 |
2 – 8 |
600°C |
High toughness, corrosion resistance, low coefficient of friction |
Plastic injection mold cores, cores, scrapers |
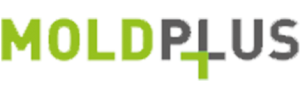 |
TiCN |
Magenta-grey |
3800±200 |
0,25 |
2 – 4 |
400°C |
High hardness, high wear resistance and low friction coefficient,improved toughness, lubricating properties |
Plastic injection moulding, cutting, forming |
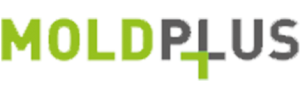 |
TiCrN |
Dark golden yellow |
3400±200 |
0,35 |
2 – 5 |
600°C |
Excellent toughness, low coefficient of friction, high hardness, high resistance to workpiece sticking and wrapping |
Plastic injection mold cores, cores, scrapers |
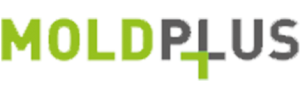 |
AlTiN |
Anthracite |
3400±200 |
0,7 |
2 – 6 |
900°C |
High hardness, high toughness, high temperature resistance, high hot hardness |
Plastic injection mold, cores, pin, pushers, scrapers |
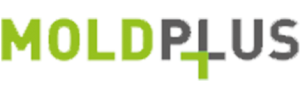 |
ZrN |
Light yellow |
3000±200 |
0,35 |
2 – 5 |
600°C |
Excellent surface properties, very high adhesive wear resistance, very good corrosion resistance, |
Plastic injection mold cores, cores, scrapers |
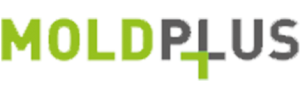 |
Patent |
Silver gray anthracite |
3400±200 |
0,35 |
2 – 8 |
600°C |
High toughness, corrosion resistance, low internal stress, low coefficient of friction, high wear resistance for copper-beryllium alloy |
CuBe2 – copper-beryllium alloy; plastic injection mold cores, cores |